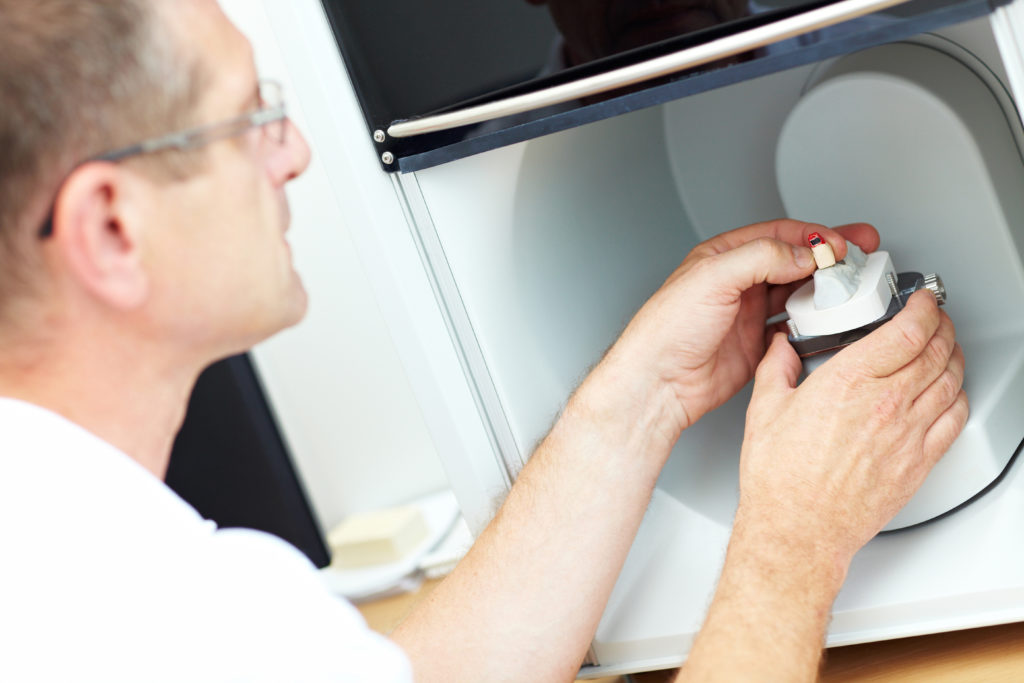
3D Printing Areas of Application
Customized Series Production
Produce unique objects in series – 3D printing makes it possible. For dentistry, several individual implants are now being printed in one process, which significantly reduces the unit price. Spare parts for cars that are normally no longer available on the market can also be reconstructed if required. Additive manufacturing enables the consideration of specific customer requirements in largely unchanged economic conditions and is thus increasingly becoming a relevant technology in production for industry 4.0.
Rapid Prototyping/Rapid Tooling
Thanks to additive manufacturing directly from 3D CAD data, rapid prototyping allows prototypes and display models to be produced in the shortest possible time. As 3D printing, unlike ablative processes such as milling or turning, does not require any special tools for production, the manufacturing process can be fully standardized. This significantly reduces the development time from the idea to the production-ready article („time-to-market“). If potential for improvement is identified in a testing phase, changes can be transferred to the 3D model and implemented without delay – a further advantage in product development. Transparent components can also be integrated, so that internal functions can be visible to the viewer.
Currently, the classical machining processes are still used for rapid tooling, which enable significant time savings in tool production through the use of standards and standardized parts in the design, manufacturing and assembly processes. When it comes to the implementation of particularly complex geometries, 3D printing already produces master models and tool inserts for various injection molding processes. A significant strength of injection mold inserts and components manufactured using additives is, for example, the integration of near-contour cooling channels, which can reduce the cycle time in series production and improve the quality of the products.
Application in Hobbies
Until a few years ago, 3D printers were almost unaffordable for private use. Today, powerful FDM printers are already available from about 1,000 €. They process strand-shaped plastics (filament), which are mostly based on thermoplastics such as PLA (polylactide acid) or ABS (acrylonitrile-butadiene-styrene). The compact units can be installed in any room. Currently, Fused Deposition Modeling is the only 3D printing method available for home users.
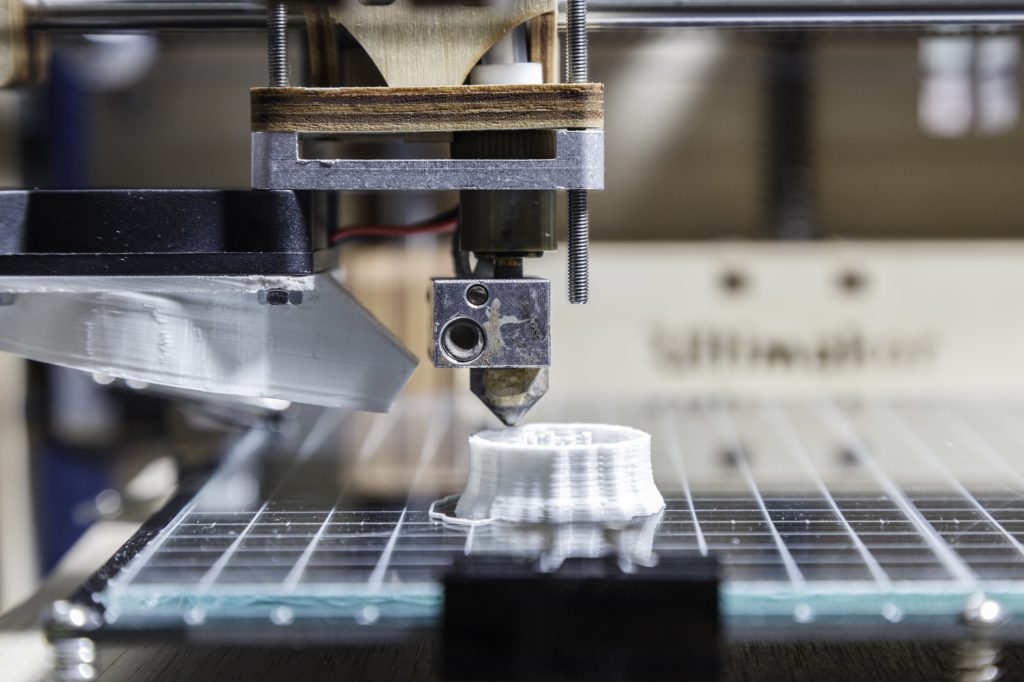