Selective Laser Sintering
In selective laser sintering (SLS), powdery materials made of plastic are constructed into functional and mechanically robust 3D objects. Due to the currently still very high prices for SLS production lines, these are often found in the industrial environment.
The powder is applied thinly to a build platform using a squeegee or roller. Based on the coordinates from the existing STL file, a laser melts the material at the corresponding points. Next, the platform is lowered by the value of a layer thickness, and the process repeats itself until the completion of the object. Simultaneous production of several makes is also possible.
In the construction chamber, the material is heated to just below the melting point, so that a low energy output of the laser is sufficient to trigger the melt. During production, the component is supported by the powder bed surrounding it, which means that no additional support structures are required – a major advantage that offers great freedom in the design of 3D models.
Selective Laser Melting (SLM)
Selective laser melting is based on the same process as selective laser sintering, but only metal powders are processed here. The powerful laser melts the material at temperatures of up to 1,250°C in the laser focus. Since the construction space is not or hardly heated during this time, undesirable effects such as curling, warping or burns can occur due to the large temperature difference. A support structure attached to the base plate counteracts this but must be removed manually after the manufacturing process.
Selective laser melting is suitable for the production of 3D objects from tool steel and stainless steel or aluminum. Thanks to technological advances, it is now also possible to process copper using the SLM process. The metal is an important material for industry due to its excellent electrical and thermal conductivity, but its use in 3D printing is made more difficult because of the same properties. Highly-conductive copper is currently only processed by PROTIQ.
Stereolithography (SLA)
High-resolution plastic components can be produced in a short period of time even with the oldest of all 3D printing processes, which is why the technology has established itself primarily in the field of rapid prototyping. Highly-detailed 3D objects with wall thicknesses from 0.1 mm are created from liquid photopolymers (e.g. epoxy resin). A UV laser cures the material layer by layer using CAD-based coordinates. The print platform is then lowered into the plastic bath by exactly one layer thickness so that the next layer can be irradiated by the laser. Although the material changes from a liquid to a solid state, the material is not yet stable: The complete curing process requires a further step, in which the component is exposed to UV light again. Subsequent processing is usually not necessary since the surface of the objects is very smooth from the very beginning.
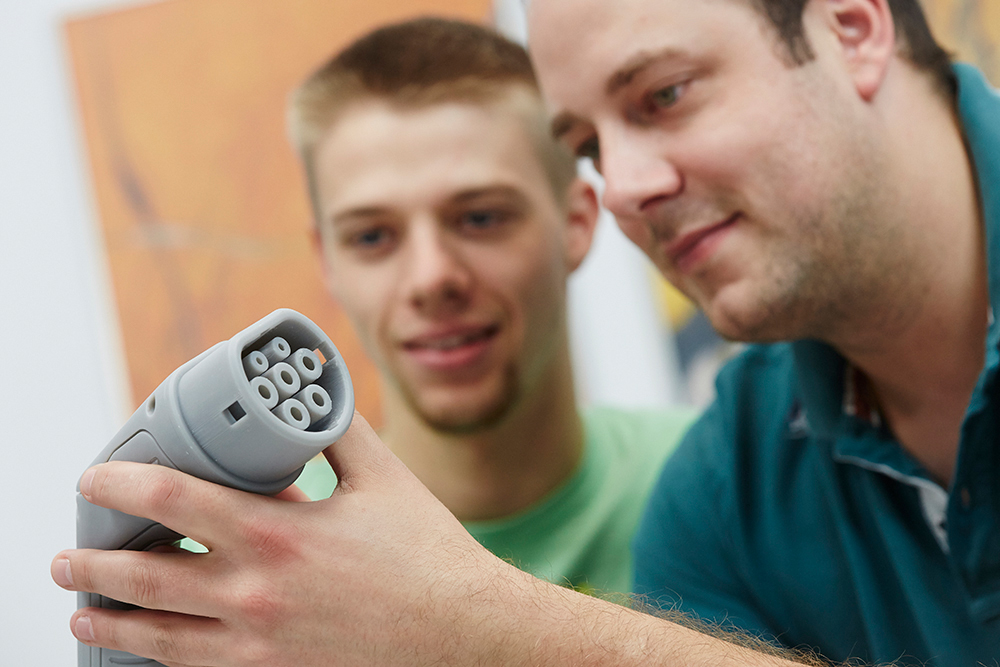
Lithography-Based Ceramic Manufacturing (LCM)
In addition to plastic and metal, ceramics is the third largest material group in 3D printing. In additive manufacturing, this material is processed in a multi-stage process to produce 3D objects with the typical ceramic density. First, a liquid ceramic monomer suspension is built up into a green body in the stereolithography process.
For this purpose, the build board is lowered into the liquid and cured layer by layer locally with UV light. The polymers are then removed from the green body via pyrolysis since they were only needed as binders. Finally, the 3D object passes through a sintering process to compress the ceramic particles.
PolyJet/MultiJet Modeling (MJM)
The PolyJet process is similar to conventional inkjet printing. The print head moves over the build platform and sprays fine droplets of a liquid polymer. At the same time, the material is irradiated with UV light and thus crosslinked or cured. In addition to various thermoplastics, the MJM uses waxes, which are built up into support structures for the 3D object by an additional print head. The use of more than two print heads allows the production of multicolor components and the use of different materials in the same manufacturing process.
Fused Deposition Modeling (FDM)
The so-called FDM printers are increasingly finding their way into private households. They process strand-shaped plastics, so-called filaments, which are fed into an extruder, melted down and applied layer by layer to a build platform. Many FDM printers are equipped with a heating bed so that the object does not warp during cooling. The temperature of the 3D model is slowly and evenly lowered to prevent large tension differences.